By Paul Reed
Your shipping and receiving area benefits from smart space planning, just as other areas do. And in some cases, it’s about more than raising productivity – it can be a safety issue as well.
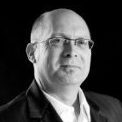
The Showroom Guy
info@theshowroomguy.com
The public-facing parts of your jobber store aren’t the only areas that benefit from intelligent space planning and organization. The shipping and receiving area is one part of the store we, as store designers, have been looking at more and more in recent years. Keeping it clean, well thought-out and organized can result not only in time savings and improved productivity; it can also improve safety.
Your shipping and receiving area is always a fast-moving area, with people coming and going constantly. I have one customer in Gatineau that has 32 vehicles coming in and out every day! With that much traffic, it’s important to take time to plan how the space can be used to maximum efficiency and convenience, without compromising safety.
Your main shipping and handling area should work like a well-oiled machine. There should be enough room for workers to move around and do their jobs without bumping into each other or having to step over anything, and for trolleys or rolling bins to be manoeuvred easily. Each shipper should have all the equipment he or she needs to quickly and efficiently package, label and log items going out, close at hand and easy to keep organized when not in use.
Keeping the entire area clean and clutter-free at all times is very important. Avoid leaving deliveries or other items out on the loading dock any longer than absolutely necessary; it should always be a priority to log and process deliveries as soon as possible after they arrive.
The way products are arranged in the warehouse or storage area can make a huge difference in the efficiency of this area for workers. One way to look at it is to think of the warehouse as being like a very large showroom. Products should be organized by type or department, with the most popular items at the most accessible levels, and less common items arranged progressively to either side and above and below. (Some warehouses store by SKU, brand or other divisions; but I’ve found that like-with-like is more intuitive, which is ultimately more efficient.)
The most popular and fastest-moving products should be stored at eye level and near the front, to save steps picking and carrying them to the shipping area. If you have regular customers who routinely pick up several shipments through the day, you might reserve a special area in front, near the shippers’ station, for them.
At least as important as how you arrange product storage is the construction and layout of the warehouse itself. Much of this has to do with safety, not just efficiency, and this should be a paramount concern to staff at all times.
First of all, ensure that the aisles are always wide enough for forklifts to manoeuvre safety and easily. Even a minor bump can throw off the weight distribution of a large rack of products, with potentially disastrous consequences. (I’ve actually seen entire rows of warehouse stacks tumble like dominoes.)
Having bright enough lighting that illuminates all parts of the warehoused eliminates shadows falls in this category. It’s surprising how much improvement to a working environment comes from simply being able to see what you are doing (and where you are going), and yet I still occasionally cows across warehouses with rows of dim, half burnt-out eggshell fluorescents hanging high overhead.
Also, it’s critical to have appropriate racking for the weight of the parts that will be stored in the warehouse. Don’t cheap out on weight tolerances; you could be courting disaster here too. (This is especially important if you use palette racking, which routinely houses very high weights of product.) Make sure all your staff is thoroughly trained not only in where to find products in the stacks (or to store them when deliveries come in), but the maximum weight capacity of the shelves, to ensure they are not overloaded.
Inspect the shelving regularly, perhaps with a once-daily walkaround, to check that products are stored safely and properly, that no boxes are askew or hanging, and that everything is in good order. Inspect beam uprights for any damage or weaknesses; installing bump guards against wayward forklifts might be a good idea. Combine your daily walkaround with a once-yearly inspection by a professional warehouse inspector (in some cases this may be required by your insurer).
Finally, keep in mind that safety is paramount in this part of the store. Every person who works in this area should be properly attired with safety vests, protective boots and, if needed, safety glasses and work gloves; in some cases, a hard hat might be a good idea too.
In a busy jobber store, people are coming and going quickly, focused on the task they are performing. A well-designed and well-planned shipping area can actually make it easier to get things done in safety, convenience and comfort – which will maximize the productivity of everyone who works there.
0 Comments